
STAYING SAFE
Crystalline silica is a mineral found in some manufactured products like bricks, concrete, tile and engineered stone. Crystalline silica dust is made up of very small particles. These particles can easily be inhaled and make their way into lungs.
The health effects are dangerous and can include silicosis where there is irreversible scarring of lungs, lung cancer, and kidney disease. Workers who are exposed to crystalline silica dust can have irreversible damage or even die from its effects.
Crystalline silica is used throughout construction and the manufacture of building products. It’s not just in engineered stone. It can be found in manufactured materials like fibre cement sheets, bricks, tiles, and cement.
Workers can be exposed when undertaking work like excavation or tunnelling through certain rocks. This is because crystalline silica is in rocks and rock products like marble, limestone, slate, shale, granite, natural sandstone, mortar and concrete.
PRODUCTS TO KNOW ABOUT
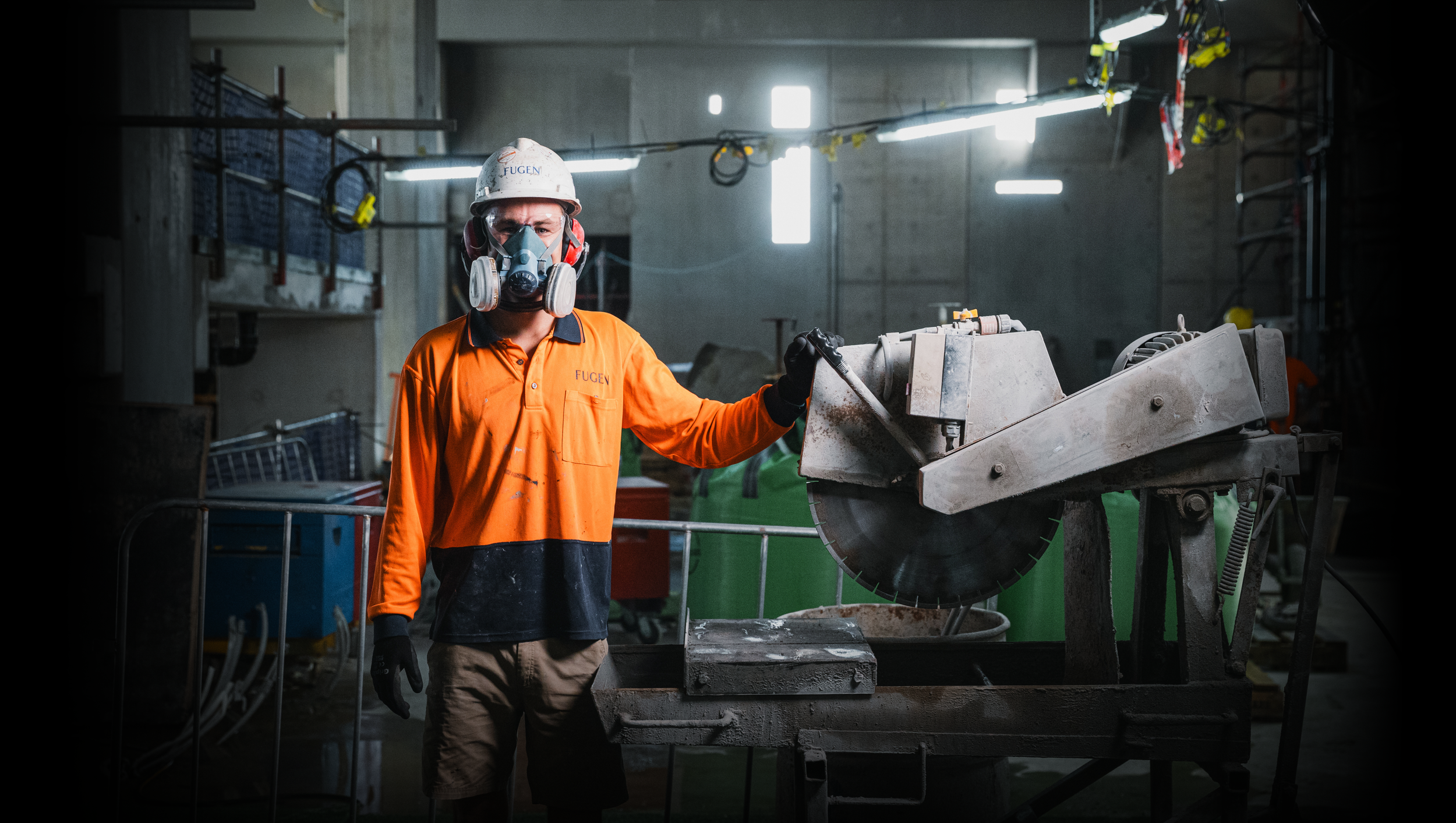
CONTROL MEASURES COULD SAVE YOUR LIFE
CONTROL MEASURES
Not all control measures are created equal, this is why we have a hierarchy of controls from most to least effective.
If the material that you are working with cannot be eliminated or substituted with another product then the remaining controls should be used.
Every worker and employer should understand that Personal Protective Equipment (PPE) is the least effective form of controlling dust exposure and relies on correct fit and use by worker as well as adequate supervision by management.
This does not mean that PPE and Respiratory Protective Equipment (RPE) should not be worn while working with silica product.
-
Wet cutting or water suppression: Using water to prevent dust from being released into the air during cutting or grinding.
Local exhaust ventilation (LEV): Using systems to capture and remove dust, fumes, or gases at the source.
On-tool dust extraction: Using tools that are designed to capture dust at the point of generation.
Automating tasks: Using machinery or equipment to perform tasks that would otherwise involve manual handling of materials that generate dust.
Enclosing processes: Isolating or encapsulating processes to prevent dust or other hazards from escaping.
Using industrial vacuum cleaners with appropriate filtration: Using vacuums to clean up dust that has been generated.
It’s important to note that any uncontrolled processing of a crystalline silica substance (that contains at least 1% silica by weight) that generates silica dust, including cutting, grinding or polishing with power tools or other mechanical plant, is not permitted.
Keep in mind that introducing some of these controls may inevitably introduce other hazards such as increased noise and vibration levels at your workplace, which will require additional mitigating control measures.
-
Planning cutting tasks to make sure the minimum number of cuts are made.
Written rules and policies for working with a CSS or cleaning CSS waste. For example, having a written clean-up procedure and log.
A maintenance schedule and log for equipment and personal protective equipment.
Limiting the length of time a worker may be exposed to RCS.
Restricted area policies so that only staff who are carrying out a task that generates RCS are allowed access to those areas.
Signage at the workplace highlighting there is a dust hazard and any required use of respiratory protective equipment and other personal protective equipment.
STAYING SAFE
PPE AND RPE

THE BAN ON ENGINEERED STONE
Following a campaign led by the CFMEU, involving unions, hygienists, health professionals, and academics, Federal and State and Territory Governments have taken decisive action to reduce worker exposure to crystalline silica dust.
The Federal and State and Territory governments agreed to introduce a ban from 1st July 2024 on the use, supply, manufacture, processing and installation of engineered stone benchtops, panels and slabs.
Engineered stone is commonly used in kitchen benchtops and comes in the form of slabs and panels which are then cut to size in factories and workshops.
Under the model WHS regulations engineered stone is defined as: an artificial product that contains 1% or more crystalline silica, is created by combining natural stone materials with other chemical constituents such as water resins or pigments, and becomes hardened. (Reg 529A) Processing includes crushing, cutting, grinding, trimming, sanding, abrasive polishing and drilling using power tools or other mechanical plant.
Note that porcelain products and sintered stone products are not included in the ban, nor does it apply to bricks, pavers, ceramic wall and floor tiles, roof tiles and other specified products. However, these excluded products are covered by the new regulations on working with crystalline silica substances.
The Federal Government has also introduced an import ban to prohibit the importation of Engineered Stone, effective from 1 January 2025, and has given customs the power to seize any product that lands in Australia.
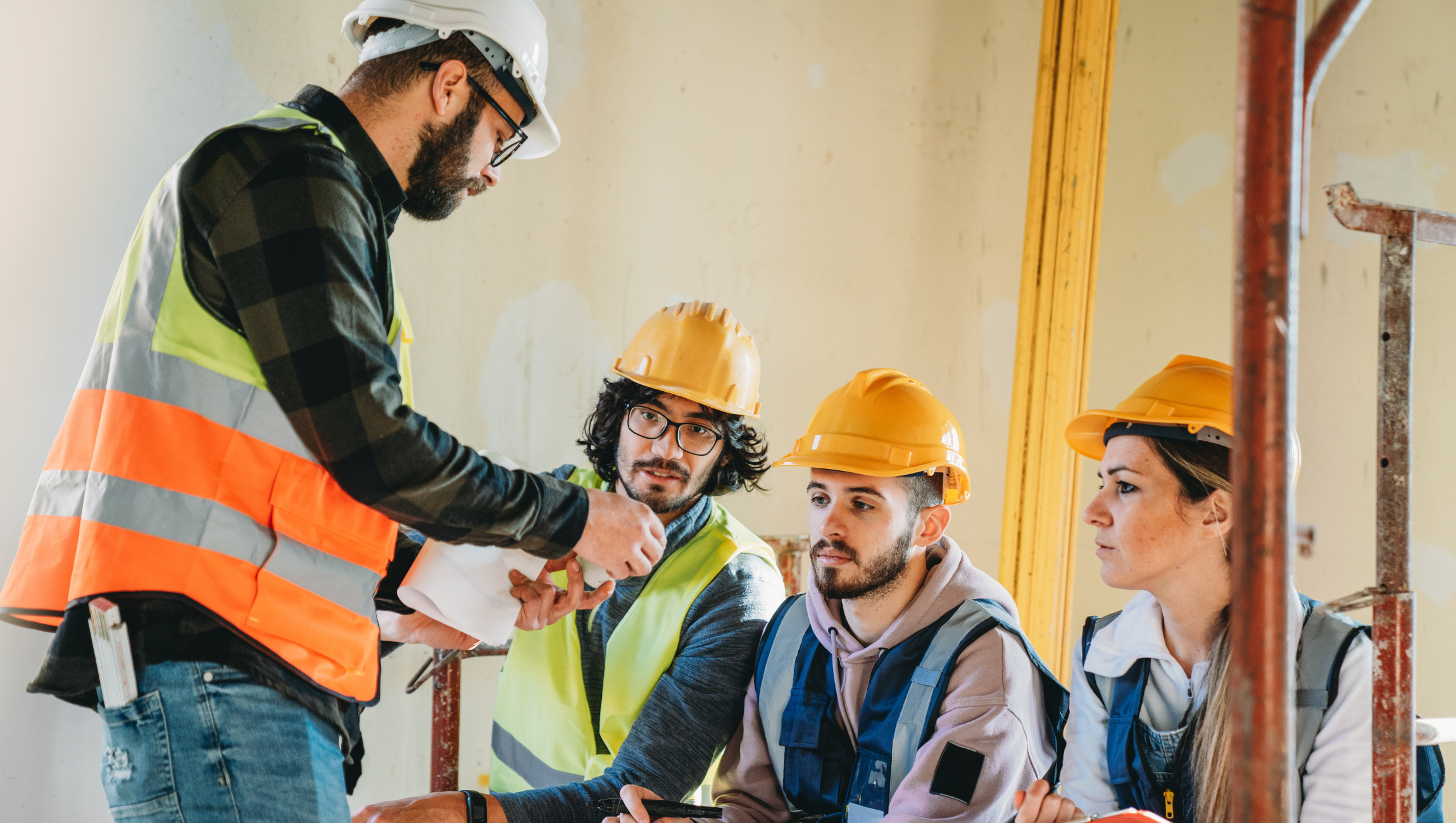
TRAINING AND MORE
LEARN MORE
Under the model WHS regulations all workers who perform high risk crystalline silica work (or who may be exposed to RCS because of the work) must receive silica awareness training that is nationally accredited or approved by the WHS regulator. The CFMEU takes a much stronger position and recommends that all construction workers receive silica awareness training as provided for in the nationally accredited course 10830NAT Course in Crystalline Silica Exposure Prevention. This course is available through the RTOs listed below (for more state specific training please contact you CFMEU organiser, delegate or HSR):
-
Creative Safety Initiatives – RTO ID: 88216
(nationally accredited - 10830NAT)
-
-
-